
Dials are held securely with tiny, soldered-on feet that are individually added to each and every piece and then refined. Tolerances measured in thousands of a millimeter are to be taken into account when installing these barely visible cylinders of metal. Each of these is then to be fine-tuned by hand to ensure that the blank is in a refined state as it advances on to the next procedures.



Countless steps are involved in the dial manufacturing process that the average person would likely not even realize. Take, for example, this Glashütte Original Seventies Chronograph Panorama Date. The two sub-dials — one for the running seconds and power-reserve indicators, the other for the 30-minute counter of the chronograph — feature a concentric pattern, whereas the main dial displays a subtle and highly refined sunray brushed decoration. Both sub-dials are hand-painted with a special masking material so as to protect their surfaces, while the sunray pattern on the main dial is being applied. This type of masking is applied to different parts of the dial at different stages of the surface treatments, numerous times over and, although the versatility of the finished dial’s decorations remains a solid hint to those in the know, most all of this effort remains painstakingly performed, yet undiscovered.


The finer details of other dials, such as the most recently introduced 2019 version of the Glashütte Original Sixties Annual Edition, are created using other creative methods. This unique dial pattern was inspired by timepieces that are part of Glashütte Original’s heritage — in this instance, dating back to the 1960s. First, a flat, blank piece of dial is made, using the aforementioned pressing method, followed by the use of a specially produced tool that is capable of stamping this complex pattern onto the blank. It is only after the tiny “islands” of the pattern have been transferred that the dial gets curved: Its edges are bent downward to highlight a much more three-dimensional and equally vintage flair.



Once that’s done, the trademark recessed indices — present on Glashütte Original Sixties collection watches, including the annual edition — are added. As seen above, this highly precise machine is capable of carving out very neatly defined sections of the dial, forming the 1-2, 4-5, 7-8 and 10-11 indices from rectangular, continuously deepening “valleys.” To be appreciated here are the tolerances with which this task is performed: The dial blank is only a few millimeters thick, so to carve into that material without weakening it or milling straight through it requires frequent checks and calibrations — and the operator’s appreciation of the amount of work that has already gone into getting the workpiece to this stage.


Yet, other types of indices are crafted entirely by hand. The Sixties Annual Edition — pictured above in fiery orange for 2019 — features the aforementioned diamond-cut, recessed indices, along with a combination of transfer-printed Arabic numerals and hand-applied luminescent pips. On every dial, each of the twelve luminescent dots at the edge of the periphery of the dial is applied by hand, under a microscope for enhanced precision.

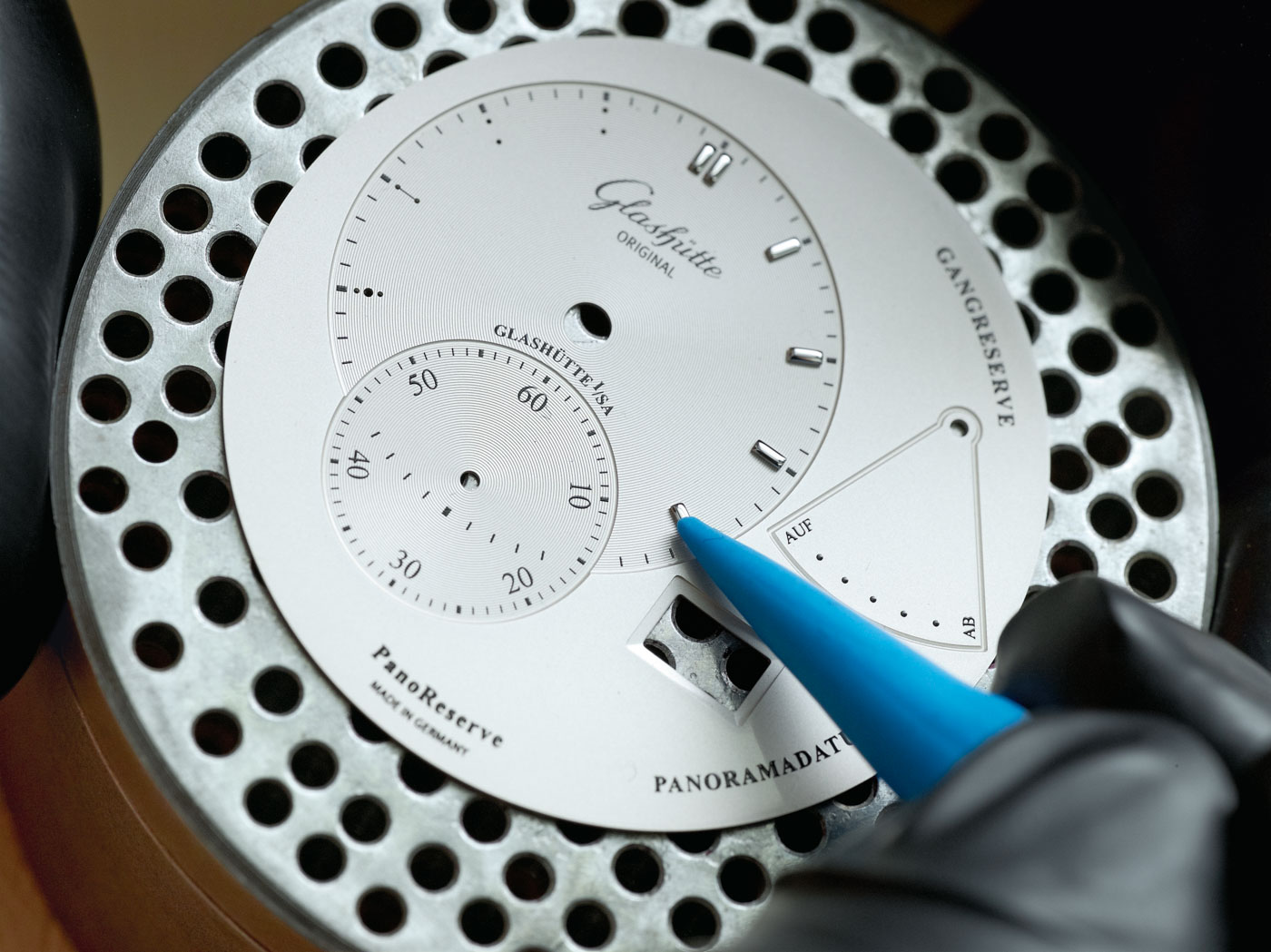
The tiny ingots that make up the indices of the PanoReserve (pictured above) are also hand-applied. Each index is secured with almost microscopically small feet that go through the pre-cut holes of the dial. These feet are then to be soldered on to the flip side of the dial with any excess material carefully removed to ensure a flat, accurate fit against the dial side of the movement below.


Some sections of dials require the dedicated attention of specialized craftspeople. Seen above is the moon phase arch on the dial of the PanoMaticLunar. The arch displays multiple subtle design treats, including its multi-tiered construction. The periphery of the arch is highlighted by a recessed area that surrounds it, while the moon-phase disc is peeking from a beautifully recessed aperture. To keep this difficult-to-produce and extremely complex segment of the dial — thanks to its several layers, curves, angles, and surface treatments — in line with the quality and refinement of the larger dial, it has to be masked, hand-filed, and hand-polished under powerful magnification. The finished dial is a case study in both dial design and manufacturing, as well as tangible proof that superbly delicate and extremely precise manufacturing can, indeed, yield highly emotional and truly beautiful results.


If the designers of Glashütte Original can dream a watch design, the company’s manufactories in Glashütte and Pforzheim can realize it. Seen above are some of the steps in the production of the moon-phase disc of the PanoMaticLunar. Crafted with precisely calculated teeth-profiles and cut into a surprisingly thick profile — so as to allow for a more robust and reliable setting mechanism, as well as a strong platform to carry the two applied moon discs — this gear is as refined and precious as every other dial component.

The tiny stars that will add a bit of sparkling flair to the PanoMaticLunar have been printed with a protective varnish on a polished surface, keeping their shapes specially protected throughout the galvanic process. The two moons are truly three-dimensional: their golden hemispheres are carefully cut out with a milling tool, which gives them their fine convex form. In the end, they are brought to a reflective polish by a special diamond-milling tool.

Whereas performing all this once would be an achievement unto itself, state-of-the-art manufacturing techniques are to be brought to perfection, and a dedicated team of superbly skilled craftspeople is required to ensure that every component of every Glashütte Original watch dial attains the expected extraordinary levels of excellence.
From the most minimalistic to the most complicated, every Glashütte Original timepiece owes its striking beauty and personality to the exquisite work that is performed day-to-day in the company’s manufactories. Its Pforzheim watch dial manufactory has been developed and advanced in ways to ensure remarkable levels of quality, as well as the technical prowess that allows Glashütte Original to be so creative and distinctive in its watch designs. Genuine expertise, deep-rooted respect for the tools and techniques of the trade, and absolute dedication to attaining outstanding levels of quality make the German-made, in-house-produced dials of Glashütte Original functional pieces of art.
Sponsored Content produced by aBlogtoWatch for an advertising partner is a form of article content meant to share information about a particular company through the aBlogtoWatch lens. It is not natural editorial content where aBlogtoWatch includes opinions, suggestions, or reviews. Sponsored Content is written by aBlogtoWatch for an advertiser without an editorial or opinionated angle and is meant to convey facts and media in a way that helps advertising partners share insights and views into their brands and products.